-
Pouches Packing Machine
-
Granule Packing Machine
-
Liquid Packing Machine
-
Powder Packing Machine
-
Mini Doypack Packaging Machine
-
Tea Bag Packing Machine
-
Coffee Packing Machine
-
Vertical Packing Machine
-
Flow Packing Machine
-
Stand Up Pouch Packaging Machine
-
Rotary Vacuum Packaging Machine
-
Filling Machine
-
Horizontal Doypack Packing Machine
-
Premade Bag
-
Packing Machine Accessories
-
Filling and capping machine
CE Check Weigher Detection Sorting Equipment Grouped Equipment
Place of Origin | Guangdong,China |
---|---|
Brand Name | ZCHONE PACK |
Certification | ISO,CE |
Model Number | ZC-XB1 |
Minimum Order Quantity | 1set |
Price | $5,500~$6,800 |
Packaging Details | Standard export wooden case packaging |
Delivery Time | 15 work days |
Payment Terms | L/C, D/A, D/P, T/T, Western Union, MoneyGram |
Supply Ability | 1/sets/15day |
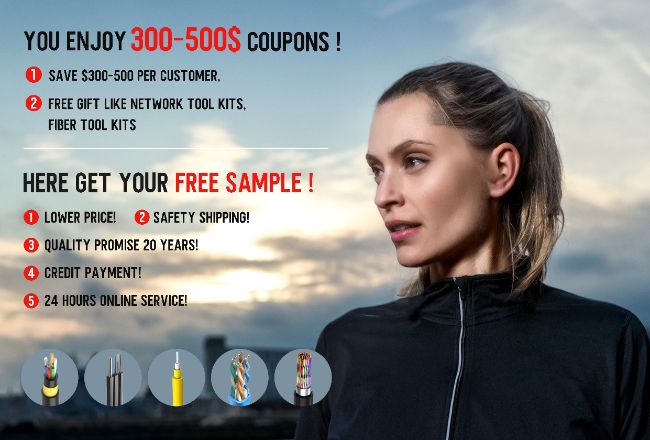
Contact me for free samples and coupons.
Whatsapp:0086 18588475571
Wechat: 0086 18588475571
Skype: sales10@aixton.com
If you have any concern, we provide 24-hour online help.
xProduct Name | Check Weigher | Speed(Bags/Minute) | 50 |
---|---|---|---|
Accuracy(g) | ±0.5g-2g | Min. Scale(g) | 0.1 |
Product Preset Programs | 20 | Dimension(mm) | 900(L)X800(W)X1300(H) |
Highlight | 50Bags/Min Check Weigher Machine,900mm Check Weigher Machine,Multifunctional Checkweigher Conveyor |
Packing Machine Type | |
---|---|
Granule Packing Machine | |
Liquid Packing Machine | |
Powder Packing Machine | |
Stand-Up Pouch Packing Machine | |
Vertical Packing Machine | |
Horizontal Packing Machine | |
Tea Bag Machine | |
Coffee Bean Packing Machine | |
Horizontal Packing Machine |
Packing Machine Accessories Check weigher Detection Sorting Equipment Grouped Equipment
Equipment Specification:
Items/Specifications | Standard weight Range |
10-2000g | |
Speed(Bags/Minute) | 50 |
Accuracy(g) | ±0.5g-2g |
Min. Scale(g) | 0.1 |
Product Preset Programs | 20 |
Dimension(mm) | 900(L)X800(W)X1300(H) |
Weight | 150KG |
Reject System | Pneumatic/Pusher/Diverter/Drop/Select |
Voltage | AC220V |
Frequency | ±10% |
Power | 50Hz/500W |
Belt Height /size | 800mm/450x300mm(depend on requirements) |
(We can provide you with exclusive customized services according to your needs!)
Weight alternative is a high-speed, high-precision online sorting equipment that can be integrated with various packaging production lines and conveying systems. It is mainly used for online detection of whether the product weight is qualified, whether there are missing parts in the package or product weight storage. The weight alternative method completes the measurement of the weight of the product during the conveying process of the product, and compares the measured weight with the preset range, and then the controller issues an instruction to reject the unqualified products or divide the products with different weight ranges to different regions.
The workflow of weighing and screening by weight alternative can be divided into four parts:
Part 1: Preparation for Weighing
The product enters the front conveyor belt of the weight alternative equipment, and the speed setting of the front conveyor belt is generally determined according to the distance between the products and the required speed. The purpose of this is to ensure that only one product is on the weighing platform during the weight alternative process.
Part 2: Weighing Process
When the product enters the weighing alternative, the system recognizes that the product to be tested enters the weighing alternative according to external signals, such as photoelectric switch signals, or internal level signals. Based on the operating speed of the weighing section and the length of the conveyor, or based on the level signal, the system can determine when the product leaves the weighing zone. From the time the product enters the weighing platform to the time it leaves the weighing platform, the load cell will detect the signal, and the controller selects the signal in the stable signal area for processing, and the weight of the product can be obtained.
Part 3: Sorting Process
When the controller gets the weight signal of the product, the system will compare it with the preset weight range, and sort the product. The sorting type will be different according to the actual application, mainly including the following types:
A. Rejection of unqualified products;
B. Eliminate overweight and underweight separately, or transport them to different places;
C. According to different weight ranges, it is divided into different weight categories.
Part 4: Reporting Feedback
All weight alternative have a weight signal feedback function. Usually, the average weight of the set quantity of products is fed back to the controller of the packaging/filling/canning machine. The controller will dynamically adjust the feeding amount to make the average weight of the product closer to the at the target value.
In addition to the feedback function, the weight sorting nickname can also provide a wealth of report functions, including the number of packages in each area, the total amount in each area, the qualified number, the qualified total, the average, the standard deviation, and the total number and total accumulation.